Offshore and Maritime installations for demanding environments
Technotron is a trusted specialist in the engineering and integration of offshore and maritime installations. With decades of experience in maritime technology, electrical engineering and automation, we offer turnkey solutions that meet the highest standards for safety, durability and functionality at sea.
Whether for a new build or a retrofit, our systems are designed to operate in the harshest offshore environments. From dynamic positioning and hybrid power systems to intelligent control panels and motion-compensated offshore access systems—we deliver complete and robust electrical solutions tailored to each vessel or offshore platform.
Application areas in offshore maritime installations
We support a wide range of offshore and maritime installations for the energy, marine and renewables sector. Typical installations include:
Offshore access systems, including motion-compensated gangways for safe transfer of crew and cargo
Power distribution systems (AC & DC) for floating production units, drilling platforms and support vessels
Ballast water and pumping control systems for vessel stability and positioning
Integrated control systems for cranes, winches and offshore hoisting equipment
Battery and hybrid drive systems, including shore power and energy management controls
Alarm and monitoring systems for critical onboard conditions (temperature, pressure, fuel levels, etc.)
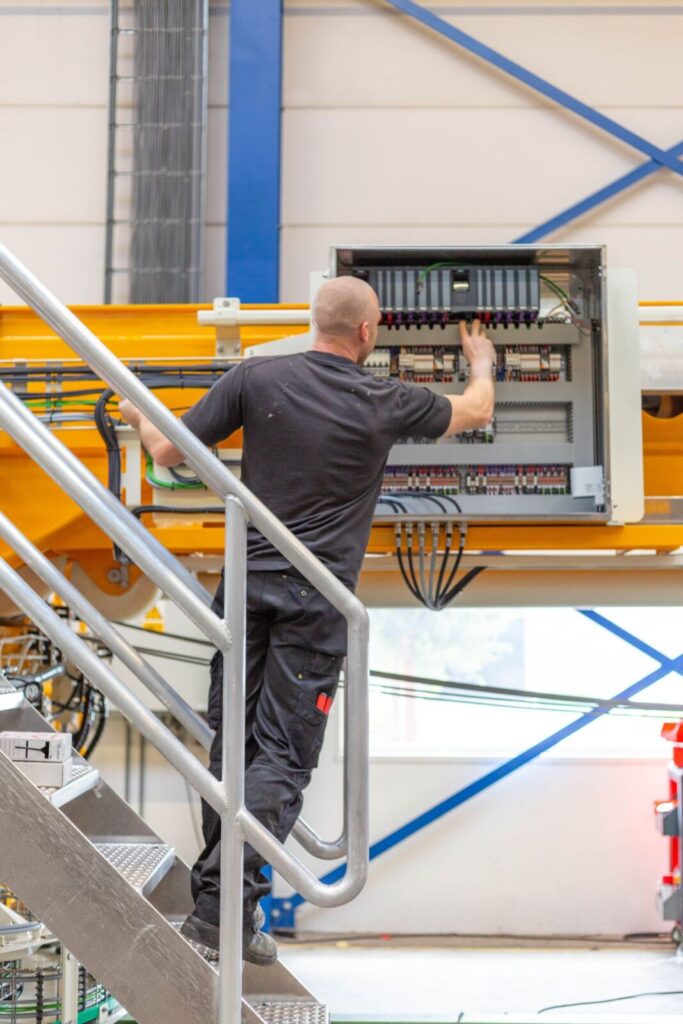
Bring to Work Offshore Access System
Together with Hydrauvision and Z-Bridge BV, Technotron is designing and installing the complete electrical installation of the offshore access system ‘Bring to Work’. Bring to Work is a unique and complex system distinguished by its redundancy. The entire device is controlled by two separate systems, both hydraulic and electrical. Both systems monitor each other and adjust if necessary. This makes the Bring to Work extremely safe to use.
The B2W system makes a safe connection from the ship to the offshore structure. Thereafter, up to four persons are driven in a lift container to the construction over the system’s mast. In addition to the people transfer function, the functionality has been extended to include a crane function. Loads up to 3 tonnes can be safely placed on a fixed offshore structure from a moving ship by the active compensation of the base of the new access system.
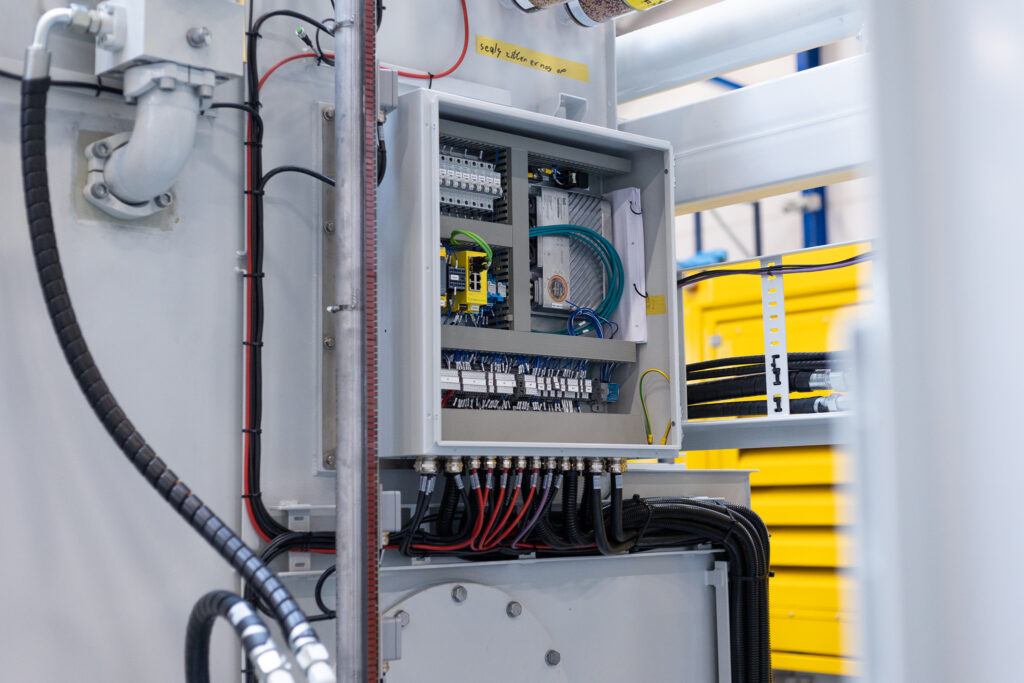
Maritime engineering with high standards
Our solutions are developed in close cooperation with classification societies (such as DNV and Lloyd’s Register) and shipyards. We apply strict standards to every maritime installation, from component selection to final factory acceptance testing (FAT).
With our multidisciplinary team of engineers, we provide high-end maritime engineering services that combine space efficiency, modular design and corrosion resistance. This ensures our systems are not only compliant, but also built to last in aggressive marine environments.
In the world of maritime technology, precision and safety are paramount. That is why we focus on detailed cabling layouts, vibration-resistant enclosures and seamless software integration—whether it concerns a tugboat, jack-up rig or cable laying vessel.
Full-service delivery for offshore installations
From design to commissioning and lifecycle support, Technotron delivers complete solutions for offshore maritime installations. We provide services to a broad range of sectors:
- Offshore wind
- Oil & gas
- Dredging and towage
- Naval and coast guard vessels
- Dive support and cable laying ships
We also support modernisation and digital transformation of older offshore installations, offering control system upgrades, energy-efficient retrofits, and integration with remote monitoring platforms.
Looking for reliable and future-proof offshore and maritime installations, including advanced offshore access systems or hybrid power integration? Get in touch with us for custom solutions.